In the last months, Fraunhofer IWKS has received sample materials from several partners. Indumetal provided pouch and cylindrical domestic batteries, while Accurec sent 200 kg of pyrolyzed and shredded domestic batteries (100 kg NMC from e-bikes/power tools + 100 kg LCO from tablets/laptops/smartphones).
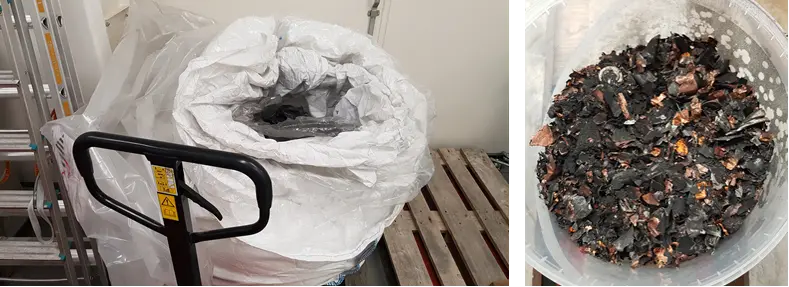
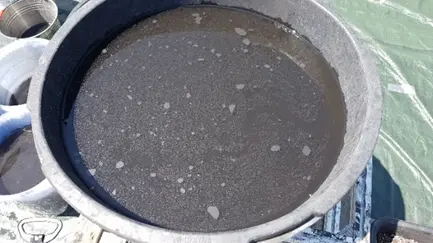
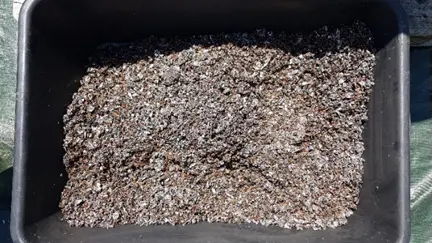
With these materials, the team at Fraunhofer IWKS has been working on a new sorting method to separate the black mass from the other fractions (plastics, Fe, Al, and Cu) and to produce black mass rich in metal content (Li, Ni, Mn, Co). After sorting, they analysed the black mass using element analytics (ICP-OES) and SEM/EDX mappings for the localization of impurities in the black mass. Furthermore, a Multiphase Carbon/hydrogen/Moisture Analyzer was used to countercheck the carbon content. Finaly, all materials remaining after the tests were sent to Indumetal for the purpose of continuing the sorting experiments.
Black mass generation, sorting and characterization
Two different methods were applied for the generation of black mass and three different sorting processes were compared for its separation. Different combinations were tested and evaluated by controlling the purity level whereas the process parameters were evaluated to optimize the mechanical treatment.
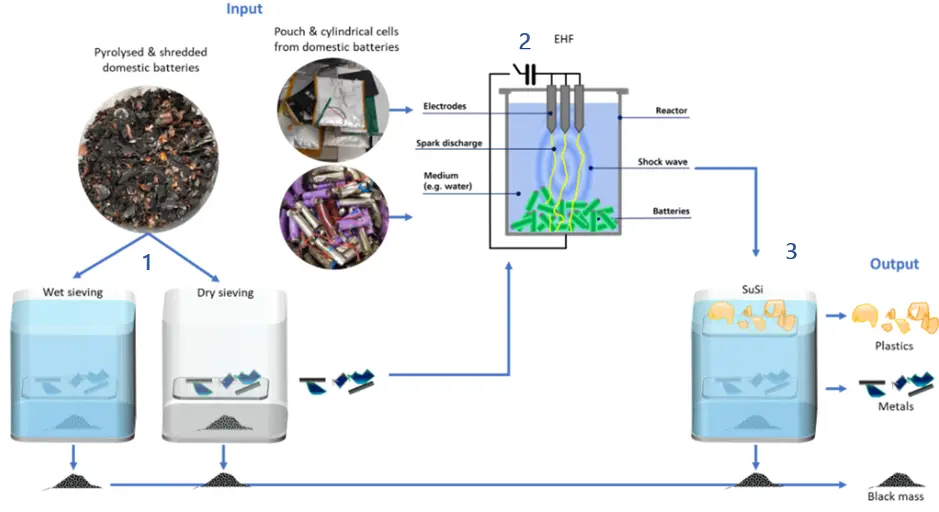
Before shipping, Accurec pyrolyzed the batteries at temperatures over 350°C under inert atmosphere to crack and decompose the organic components, but not higher than 600°C to avoid oxidation of unnoble metals like aluminium. In the following step the batteries were shredded.
In the case of the batteries received from Indumetal, the team at Fraunhofer IWKS started by comminuting the material themselves by means of electrohydraulic fragmentation (EHF). This method uses high-voltage pulses to destroy compounds at their weak points, often located at the interfaces between different materials which makes it conveniently selective.
After preparation, sorting was performed by three methods:
- Dry sieving process: (Applied to Accurec’s material) fractions were simply separated due to their grainsize.
- Wet sieving: (Applied to Accurec’s material) similar to dry sieving, but the material is mixed in water and washed during sieving. An additional EHF step was tested for the coarse fraction of the dry sieved sample, because of a lot of residual black mass sticking at the metal foils.
- Skimming & Sieving (SuSi): (Applied to Indumetal’s material) the material is mixed in water, swimming fractions are skimmed off from the top of the water bath, the sink fraction is sieved to separate fine fraction (black mass) from carse fractions (metal parts).
Finally, black mass was characterized by inductively coupled plasma optical emission spectrometry (ICP-OES) and scanning electron microscopy with energy-dispersive X-ray (SEM/EDX). In addition, a part of the material was analysed by a Multiphase Carbon/hydrogen/Moisture Analyzer.
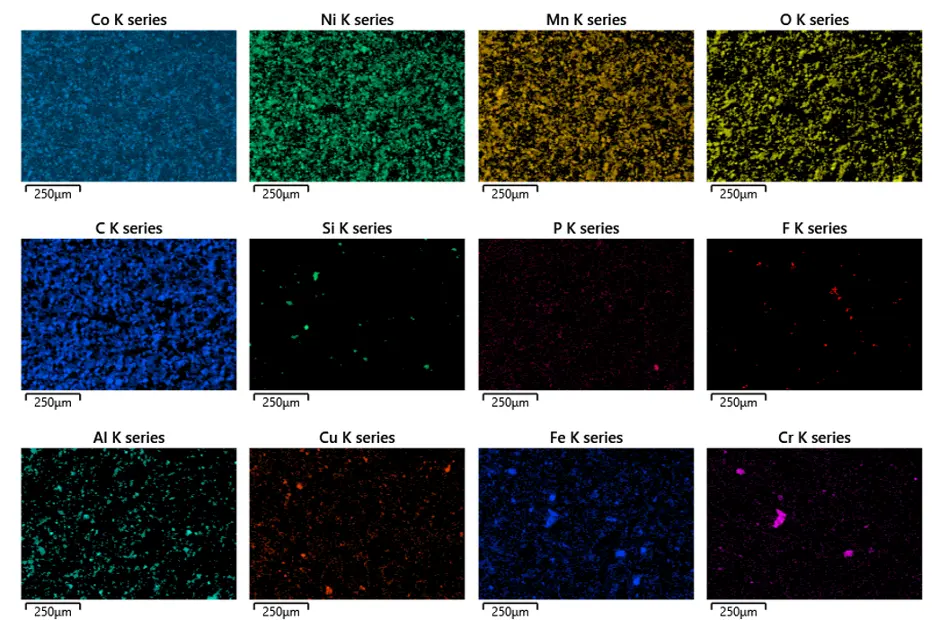
OUTCOMES SO FAR
It was found that the purity of the material was strongly dependent on the pre-conditioning. Pyrolyzed and shredded material are free from organics but still contain Fluorine and Phosphorous.
Besides the impurities, defined as the elements that are not part of the anode and cathode active materials, the active materials itself vary concerning their composition. At least the family of NMC-materials vary due to the relation of Ni. Mn, and Co.
It is challenging to keep the content of Ni, Mn, and Co constant, since the chemistry can vary between the batteries and domestic batteries do not contain more than 20-30 cells. On the other hand, EV batteries contain several thousand cells, each with the same chemistry, so that only one cell must be analysed to identify the chemistry of hundred(s) kg black mass. For currently collected domestic batteries the generated black mass must be analysed batch wise and if necessary balanced by means of mixing with other black mass. In the future the Battery Passport should enable a pre-sorting of cells, modules, and batteries by their chemistry.
Black mass from batteries treated with the electrohydraulic fragmentation showed good results. In particular, the black mass from pouch cells could be recovered with almost no loss and in good quality (less than 4% of the main impurities Al and Cu).
Finally, it can be concluded, that a complete water-based process is a very good alternative to dry processes, despite using energy consuming thermal treatment steps. By combining all the water-based steps that were applied in different sites by different partners in one line, there would be no need for drying steps in between.