During the last months, in the BATRAW project, TORRECID in the frame of Task 6.2, has synthetized at laboratory scale the best LMNO materials prepared starting from commercial precursor. We have prepared three different references, and we have sent 50g samples of each one to LEITAT and Renault in order to manufacture cathodes, built pouch cells and evaluate them in Task 6.3. All samples have been labelled with QR Code obtained through Minespider App.
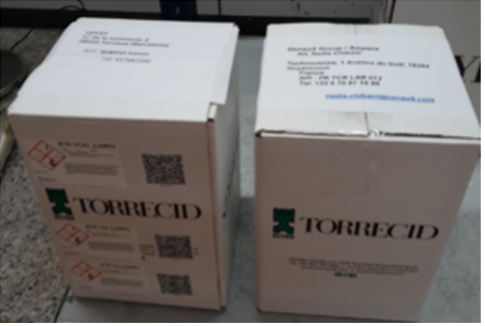
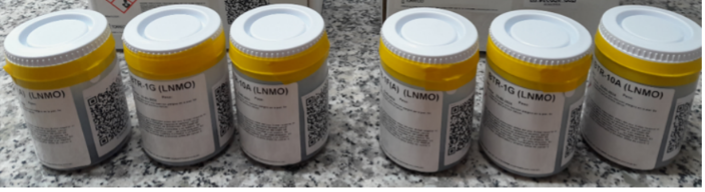
LMNO shipment sent to LEITAT and RENAULT: codes: BTR-1F (A), BTR-1G and BTR10-A 50g. of each material to each partner.
In addition, TORRECID, as WP6 leader, has coordinated with the other partners different tasks involved in this WP6 and has organized periodic follow up meetings. Finally, TORRECID has contacted ORANO (WP5) in order to know the status of preparation of recycled precursors for the WP6 partners involved in synthesis of anode and cathode active materials.
The second partner is Indumetal, who has done a study about the valorisation of the remaining fractions after battery treatment. These fractions are composed of metallic, plastic and case fractions and a little fraction of remaining black mass. In this study, Indumetal has analysed this fraction as a whole (as shown in the chart below), compared it to the typical input material they process, and, based on its composition, identified the most efficient recycling pathway within their facilities. They concluded that this material has an 83% recyclability rate. All the information and the pictures are compiled in D4.5, which has been another contribution in the end of June.
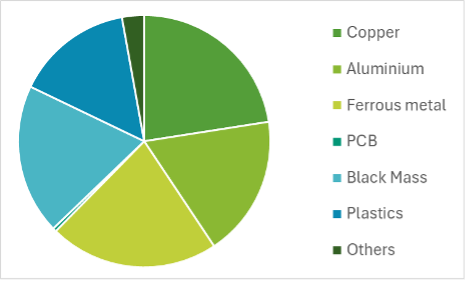
Global composition of remaining fraction.
Discharge system scale-up from 1,5 kg batteries load to 10-15 kg and working on optimisation of the process for a subsequent implementation (ongoing).
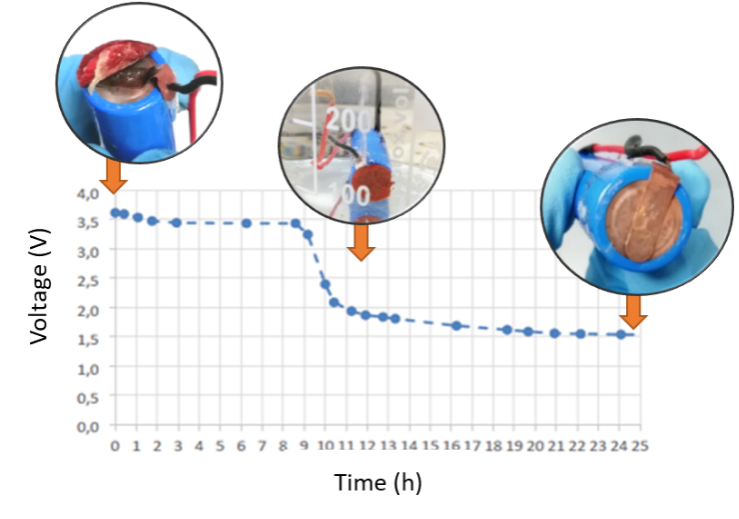
Discharge curve of a battery after the deep discharge process.
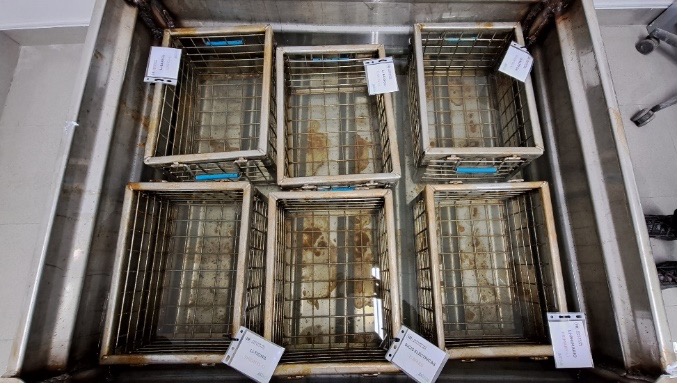
New container for the scale-up of the discharge process.
In addition, Recypilas, a company belonging to Indumetal Group, has attended this week the ICBR congress, as well as our partner Recyclia. Our colleagues have exchanged some ideas about battery recycling there.
The third partner is LEITAT, coordinator of the BATRAW Project, who has been following the progress of the different work packages. For instance, 7 deliverables have been successfully submitted to the EC portal during this period and LEITAT has actively participated with the WP3 partners to close the design for the dismantling pilot. Besides, LEITAT is involved in several WPs and some highlighted results will be detailed below:
- Automatic battery disassembly
The LEITAT Robotic team has advanced in developing AI neural networks for automatic battery disassembly, expanded their internal database, and progressed with the human-machine interface (HMI). They designed and implemented a robotic screwdriver tool, while continuing to optimize unscrewing and develop a cutting tool. Additionally, safety measures for their dismantling laboratory are being integrated into the pilot.
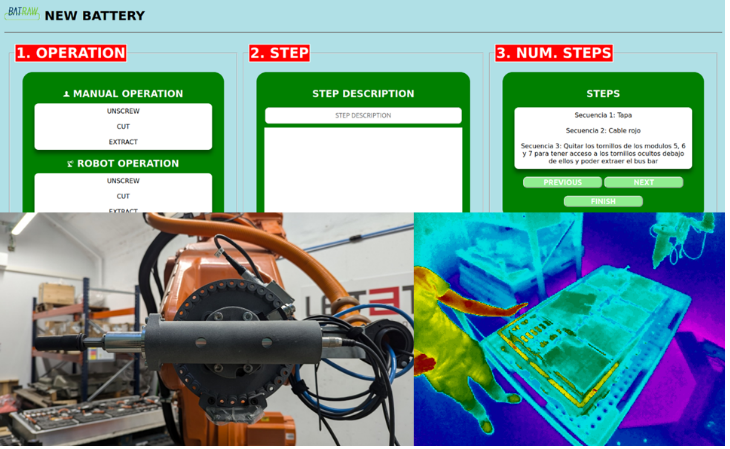
HMI (up), screwdriver implemented to the robot (down left) and IR camera for safety measures (down right)
- CRM recovery
Since the BATRAW Project began, LEITAT has focused on recovering valuable materials from battery materials, particularly Cobalt and Nickel, using polymeric inclusion membranes (PIMs). They developed PIMs with PVC and CTA, evaluating their recovery efficiency and selectivity. Recent work highlighted that maintaining a pH of 6 with a buffer drastically improved recovery, increasing it from 3% to 70%.
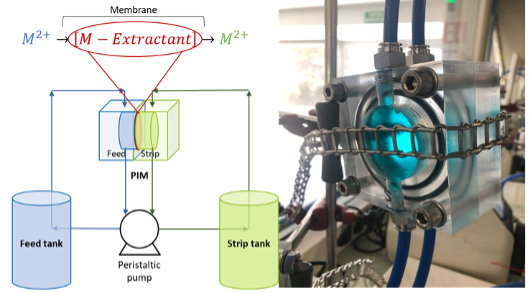
Schematic representation of the experimental set up consisting of two tanks, one for feed and one for stripping, and a pump that allows a constant flow in close loop.
The second approach targets the Li recovery via electrochemical process (ELR). LEITAT is working on lithium recovery through an electrochemical process (ELR), studying how impurities like Mn, Co, Ni, and H2O2 impact efficiency. They began testing liquors from ORANO‘s pilot and found that Mn reduces ELR efficiency, limiting lithium release.
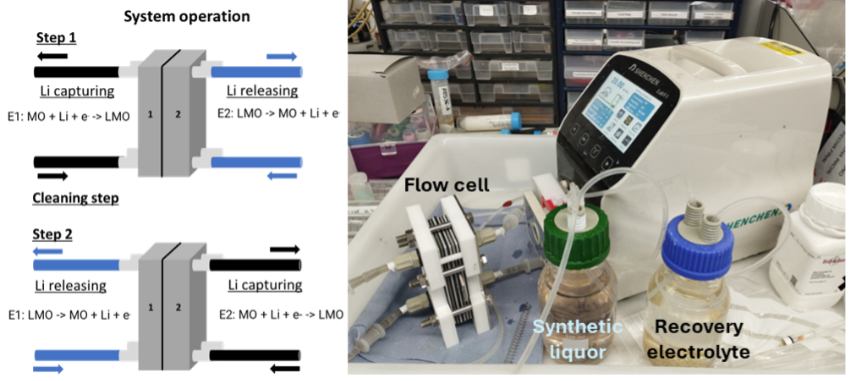
ELR Flow system.
The last approach consisted of graphite purification. LEITAT focused on purifying graphite recovered from battery materials by developing an optimized acid leaching process to remove impurities. They enhanced the graphitization degree through thermal treatment and will evaluate the recycled graphite in coin cells.
- Environmental Impact Assessment
The last activity where LEITAT is involved is the sustainability assessment. LEITAT started working on the Social Life Cycle Assessment and identified the most relevant stakeholders impacted by the project. Another achievement has been the presentation of a poster titled «Environmental performance of end-of-life scenarios of EV batteries following a life cycle approach» by Susana Leão at the SETAC Europe conference held in Seville last May.
Furthermore, LEITAT has been invited by the Health and Digital Executive Agency (HaDEA) to represent the project during the ECOMONDO (the Green Technology Expo) and discuss on Circular economy best practice for WEEE.
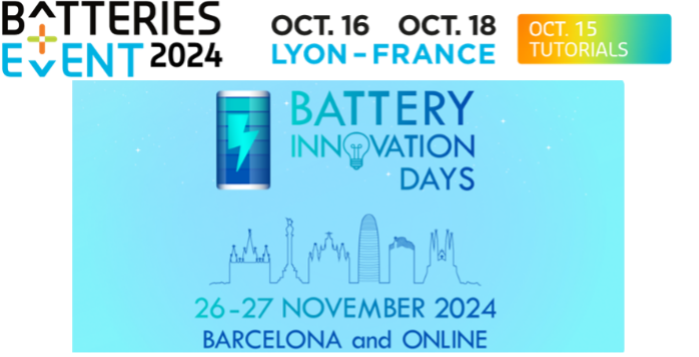
Battery event poster
Finally, LEITAT will participate in the Batteries Event at Lyon in October and the Battery Innovation Days in November where the different activities and results of BATRAW project will be exposed. Those events are part of the dissemination actions conducted by LEITAT.